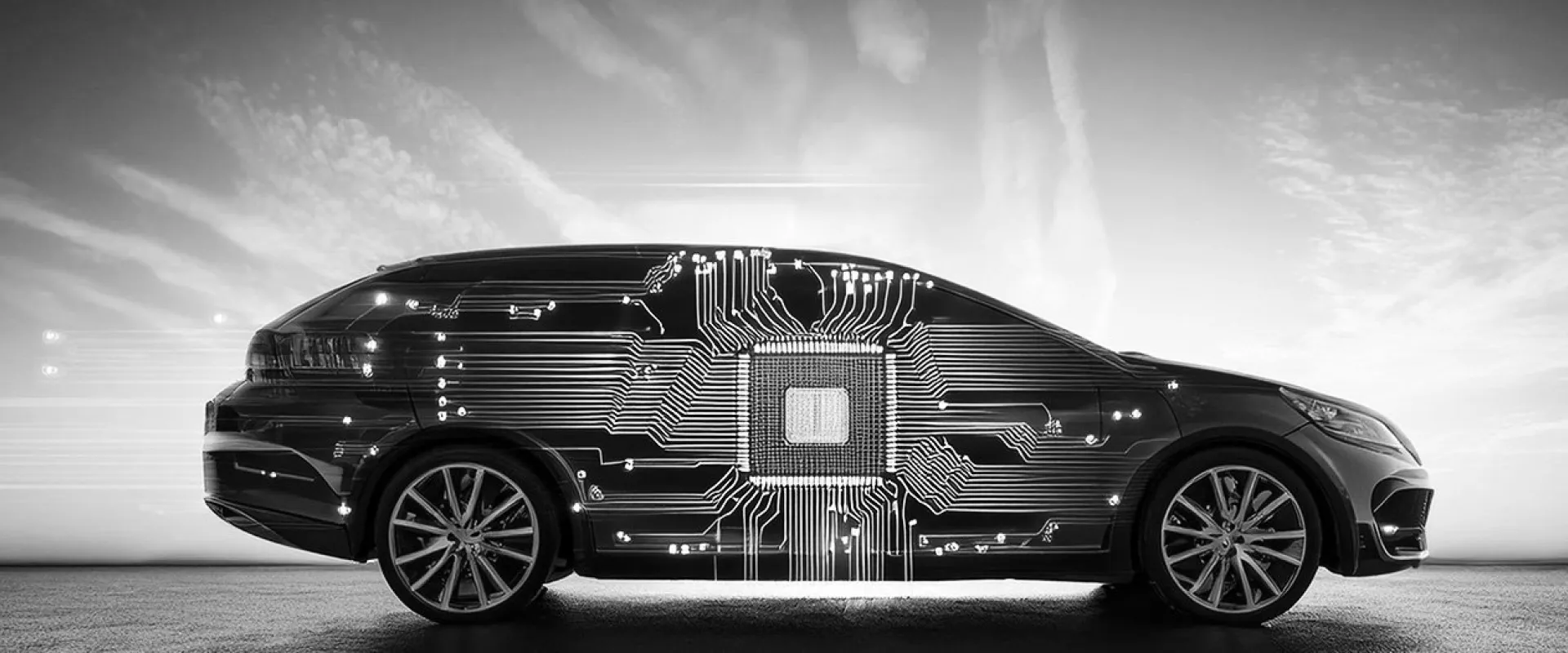
The automotive chiplet challenge
The automotive industry is going through a major transformation. Cars are no longer purely mechanical devices that move from A to B. Our cars are smarter, safer, and more connected than ever—quickly becoming ‘supercomputers on wheels’ that rely on dozens of sensors, complex algorithms and high-performance computing to seamlessly integrate driver assistance and tailored infotainment. As this trend continues, vehicles will soon require unprecedented levels of computing power, far beyond what’s feasible with conventional chip architectures.
Enter chiplets—small, modular chips designed to be combined like building blocks into larger systems, enabling high-performance computing that is both flexible and cost-effective.
This modular approach is crucial in overcoming the limitations of monolithic system-on-chip semiconductor technologies, which struggle to meet the growing demands of next-generation vehicles.
As the automotive industry moves toward this future, chiplets are emerging as the solution that offers the scalability, adaptability, and efficiency necessary to drive innovation.
How chiplets can meet the automotive challenge
Unlike monolithic chips, which integrate multiple functions into a single chip, chiplets are modular and optimized for specific tasks, such as processing, memory, or input/output. Think of them as semiconductor LEGO blocks—each block dedicated to a particular function. Blocks can be swapped in or out, allowing manufacturers to customize the system based on specific needs.
For the automotive sector, this flexibility is crucial. Vehicles today require a diverse set of technologies, from advanced driver assistance systems to autonomous driving, sensor fusion, and in-cabin infotainment. Each of these technologies has distinct requirements for computing power, memory, and connectivity. Chiplets allow manufacturers to tailor systems to meet these varying needs more efficiently than traditional chips.
Instead of designing a new chip for every feature or vehicle model, manufacturers can combine chiplets to build a platform that is both adaptable and scalable. For instance, a base chiplet design might cover standard functions like input/output and basic processing, while additional chiplets can be added to support advanced features like autonomous driving or enhanced connectivity.
This modularity not only shortens time-to-market, allowing carmakers to launch new models faster, but also helps reduce the cost of development by updating specific chiplets instead of overhauling the entire system architecture.
The automotive industry’s unique product and market space make chiplet technology particularly attractive:
Long product lifecycle and scalability
Cars have longer lifecycles compared to, for example, mobile phones, with models often staying on the market for several years. Chiplets allow manufacturers to upgrade specific components—such as adding new sensor technologies or more powerful processors—without having to redesign the entire chip for every model refresh.
As cars become more software-defined, chiplets also provide the flexibility to scale and integrate new features throughout the vehicle’s lifecycle.
Lower volumes and customization
The volume of production for a particular car model is far lower than for mobile phones, for example, which are mass-produced at immense scales. Designing and fabricating a new chip for each vehicle variant would be prohibitively expensive.
With chiplets, carmakers can build a baseline platform and customize it with additional chiplets depending on the model’s performance and feature requirements.
Automotive system complexity
Vehicles must meet stringent safety and reliability standards, which means they require far greater complexity and redundancy in their electronic systems compared to most other chip applications.
A chiplet technology platform allows manufacturers to use proven components—already validated for safety-critical functions like driver assistance or sensor fusion. This modular approach simplifies system design while ensuring that all components meet the rigorous demands of the automotive environment.
Not all car functions require the latest, costly semiconductor technology. Chiplets allow for optimized processes for specific tasks and shared resources like wiring and cooling, leading to energy savings. They are simpler to manufacture than monolithic systems-on-chip, resulting in fewer defects and higher yields. While packaging costs are higher, chiplets still offer an estimated 40% savings compared to traditional chip designs.
Obstacles on the road
While chiplets offer significant potential, their widespread adoption in the automotive industry is not without challenges. Two of the biggest hurdles are:
- Ensuring reliable, fast, and high-bandwidth integration between the individual chiplets.
- Standardizing across the sector.
Integration
In conventional chips, components are integrated onto the same piece of silicon, enabling seamless communication. However, in a chiplet-based system, these components are spread across multiple chips, requiring innovative interconnection technologies to achieve the same level of performance.
There are two main approaches for chiplet integration:
- 2.5D Integration, where chiplets are placed side by side on a common substrate (known as an interposer), allowing them to communicate through intricate wiring beneath the surface.
- 3D Integration, which stacks chiplets on top of each other to create a more compact system that mimics the functionality of a single chip.
Each method has its trade-offs. While 2.5D integration offers better thermal management and more straightforward fabrication, data transfer rates are higher with 3D integration.
For the automotive industry, 2.5D integration currently appears to be the more practical option. Its maturity, better thermal management and lower cost make it the preferential technology for most applications, especially given the industry’s strict safety, reliability, and cost-effectiveness requirements.
However, in specific areas that demand ultra-high performance and compact designs, such as in autonomous driving, 3D integration could become more suitable, if the thermal and cost challenges could be addressed.
Standardization
Another critical issue is standardization. The automotive industry requires chiplets from different vendors to interoperate seamlessly. A lack of standardized interfaces and interconnect protocols currently hampers the combination of chiplets from different sources.
To address this, the Automotive Chiplet Forum is working to create an open ecosystem that promotes standardized packaging and interconnect technologies, ensuring greater compatibility across the supply chain.
Rapid innovation cycles and resilient supply chains
Chiplets will redefine the future of automotive technology, as they enable car manufacturers to respond faster to market demands. Instead of waiting years for a new chip design to be fully developed, manufacturers can simply update or replace specific chiplets, dramatically reducing development time and time-to-market for new features.
This agility is particularly important as advanced driver assistance, autonomous driving, and in-vehicle infotainment systems evolve at a breakneck pace. The ability to quickly integrate new technologies—whether it's enhanced sensor fusion for better object detection or more powerful processors for in-cabin entertainment—gives carmakers a significant competitive edge.
The modularity of chiplets ensures that vehicle models can be updated and upgraded over time, supporting features that were not even envisioned when the car was first designed.
How star is leading the charge
For the cars of the future to become a reality, semiconductor technology must take a giant leap forward. The overarching challenge is to bring the performance of data centers into vehicles – reliably and cost-effectively. This can only be achieved if technological innovations are aligned with strategic goals of the automotive industry.
One of star’s missions is to unite key players across the automotive and semiconductor ecosystems to tackle the most pressing challenges surrounding the adoption of chiplets and ensure the automotive industry can capitalize on this rapidly evolving technology.
Moreover, chiplets promise to improve supply chain resilience. By moving away from the traditional monolithic SoC approach, which often relies on a small number of vendors with cutting-edge fabrication capabilities, chiplets allow automotive manufacturers to diversify their supply chain.
Different chiplets can be produced by multiple semiconductor providers, reducing the industry's reliance on any single supplier. This is particularly important in light of recent global chip shortages, which have exposed weaknesses in the existing system.
Looking forward, chiplets will help the automotive industry bridge the gap between current capabilities and the demands of next-generation vehicles. Whether it’s improving driver assistance, enhancing energy efficiency, or offering more customized digital experiences, the modularity of chiplets will be a key enabler of the software-defined, supercomputing-powered cars of the future.