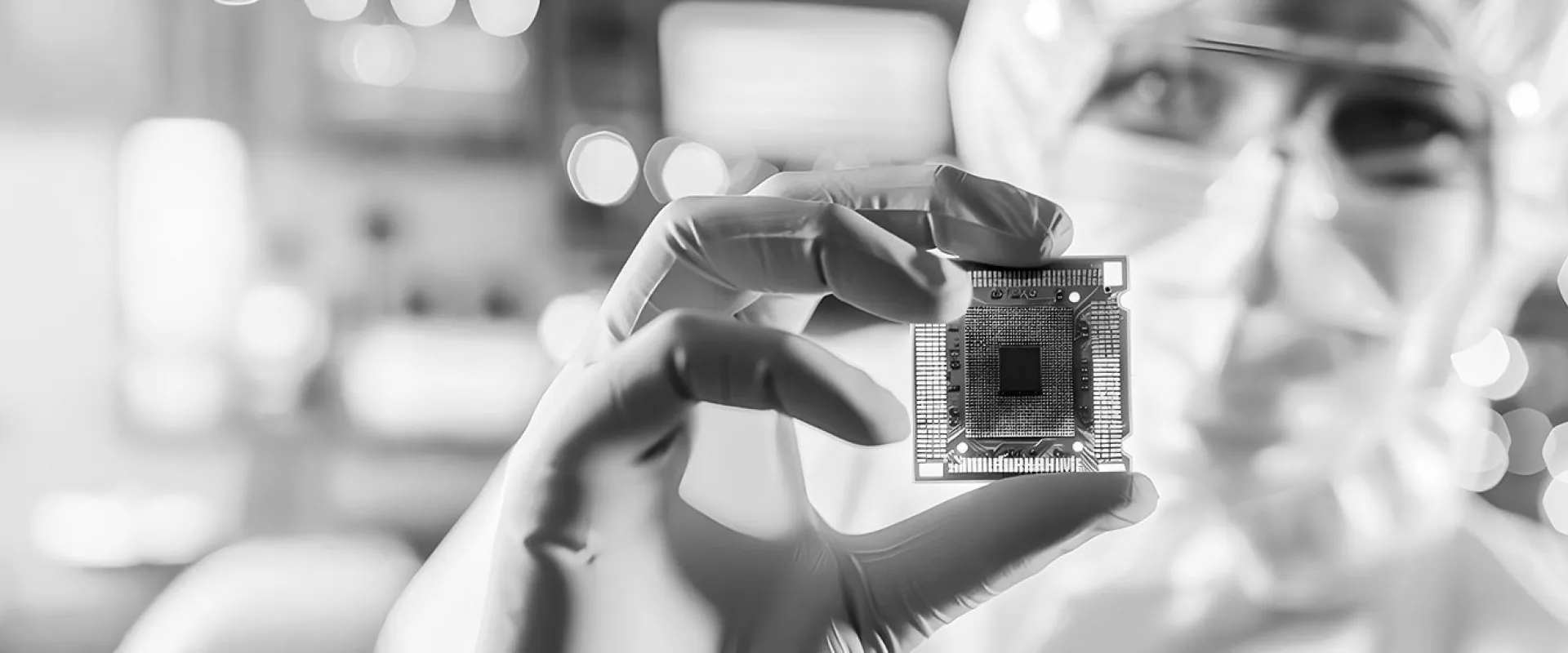
Achieving ‘zero defect’ automotive reliability with semiconductor manufacturing innovation
The mstar (Michigan semiconductor talent and technologies for automotive research) initiative has arrived at a moment of unique opportunity for the automotive and semiconductor industries.
The global automotive industry is in the early stages of a revolutionary shift away from internal combustion engines along with equally groundbreaking transformations in infotainment and advanced driver assistance systems (ADAS). The semiconductor industry’s role has never been more critical in achieving these smarter and more technologically integrated vehicles. Carmakers report that up to 80 percent of this innovation is achieved through semiconductors.
The compute and graphics horsepower required for these systems is giving rise to a new generation of AI-guided, supercomputers on wheels with up to 10,000 chips per car. Due to stringent automotive industry requirements for safety and reliability, every one of these chips must perform perfectly – every time. And recent automotive semiconductor shortages remind us how critical chips are to the entire automotive supply chain.
Automakers, tier-one suppliers and consumers alike have high standards of vehicle performance, navigation, communication and reliability. Above all, we strive to improve passenger and pedestrian safety.
Quality without compromise
Our shared challenge is to establish a zero-defect culture to meet strict standards for quality and reliability. Zero Defect is a comprehensive automotive quality initiative that extends to all car parts, including semiconductors, promoting a standard of excellence and continuous improvement.
Zero Defect initiatives in the semiconductor fab include proven process control and process-enabling technologies throughout wafer, printed circuit board (PCB) and semiconductor chip manufacturing. These inspection and metrology systems provide semiconductor makers with the data required to improve their yield – a critical metric for manufacturers, as it directly impacts their competitiveness, profitability and ability to meet customer demand.
Yield improvement is also one of the cornerstones of Zero Defect because the same defects which limit yield are typically the ones which create reliability failures in cars on the road (Figure 1).
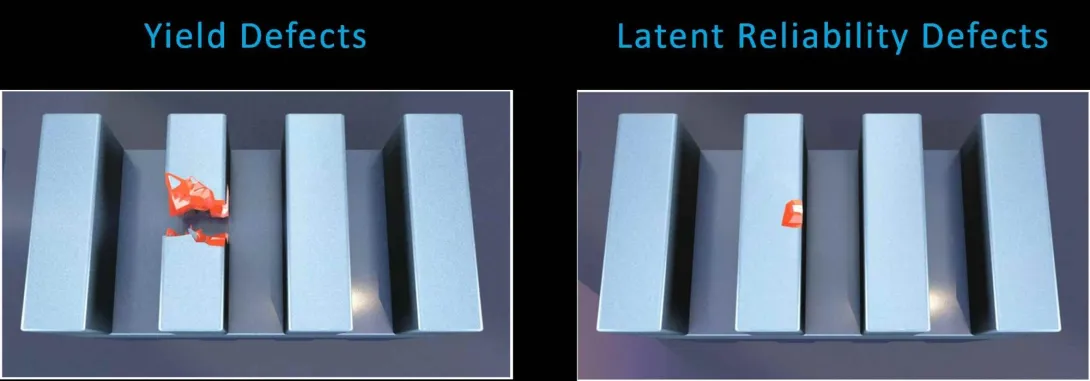
Figure 1. Yield defects fail at time zero. Reliability defects are frequently the same defect types but fail at some later time.
Zero Defect programs are becoming increasingly challenging. Most advanced semiconductor chips originate in the consumer market where a part-per-million failure rate and a life of two to five years is considered adequate. Several years are typically needed to drive the continuous improvement on consumer chips to achieve the automotive part-per-billion failure rates across a 15-year lifetime (Figure 2). The accelerating pace of automotive innovation is demanding faster adoption of more leading-edge chip technology into vehicles—and as a result the ‘comfort zone’ time lag for improving reliability for automotive semiconductors is shrinking.
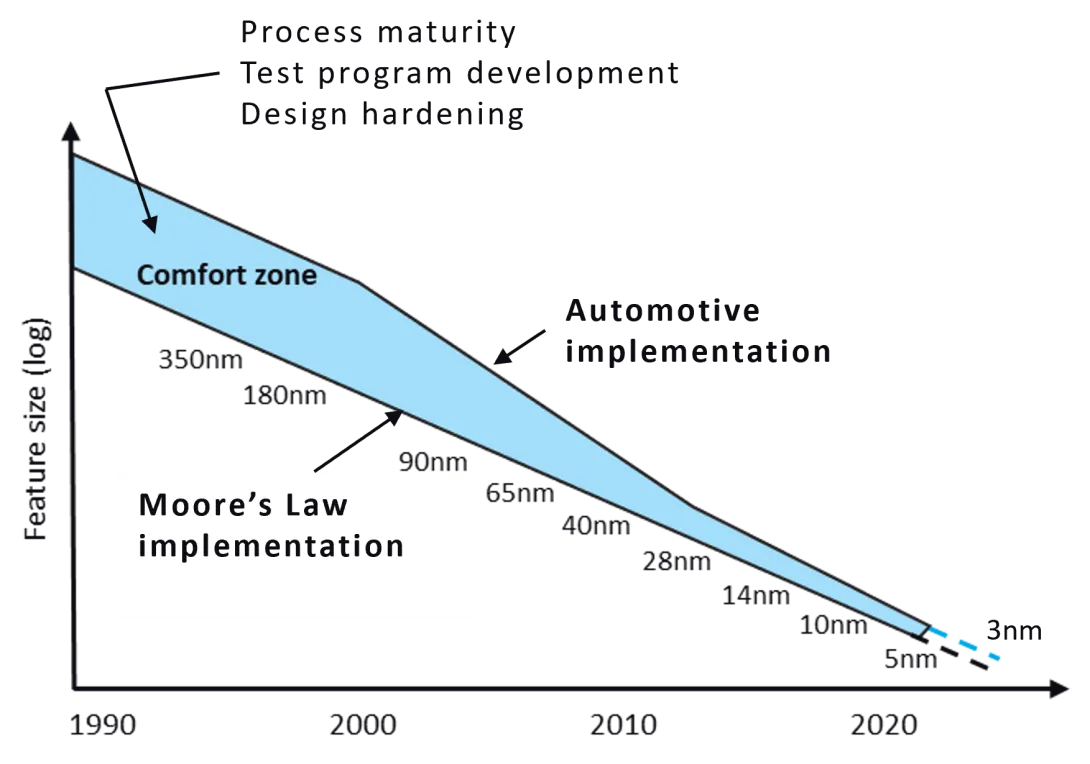
Figure 2. Zero Defect is getting harder, in part, because of the shrinking ‘comfort zone’ delay between the development of leading-edge design rule and automotive semiconductors, traditionally used for the increased reliability that comes from process maturity (Figure credit: Oliver Senftleben, BMW).
For example, automotive semiconductors will soon employ heterogeneously integrated, multi-die assemblies. The Zero Defect directive is particularly challenging for these devices since the quality must be assured for each individual die (“chiplet”) within the package (Figure 3). A defect in any one chiplet in the stack can have real-world safety implications for vehicle occupants and pedestrians. In many cases, it is difficult or impossible to completely electrically test individual chiplets since their functionality depends on connection to the other die in the package.
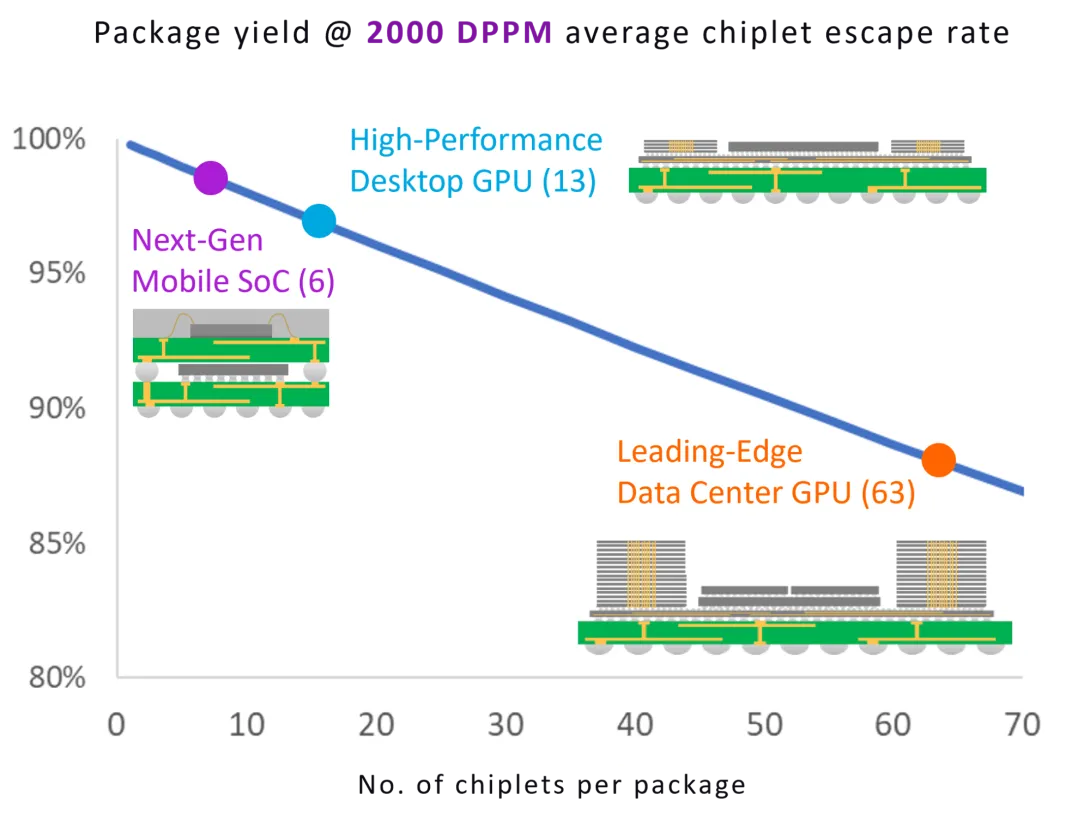
Figure 3. The known good die (KGD) problem with chiplets presents an additional challenge for automotive semiconductor reliability. Assuming 2000 defective parts per million (DPPM) is the average chiplet escape rate, yield drops with increasing number of chiplets per package.
Inline defect screening is being increasingly adopted by automotive fabs to reduce escapes for reliability sensitive devices. Screening requires inspection of 100 percent of wafers and 100 percent of die per wafer at a handful of critical inline steps. It serves as an additional safety net to supplement traditional test methods to ensure known good die (KGD). Furthermore, inline defect screening identifies potential reliability excursions at an early stage in the fab, where the cost of correcting the problem is the lowest.
KLA’s I-PAT® automated inline screening solution facilitates this task by evaluating each chip’s total defectivity at critical manufacturing steps (Figure 4). This data can then be fed forward to the quality and test engineers to be used in conjunction with electrical test data to assess die health. I-PAT, which has been recommended by automotive standards, is being used to screen automotive chips in both silicon (Si) CMOS and analog devices as well as silicon carbide (SiC)-based power devices.
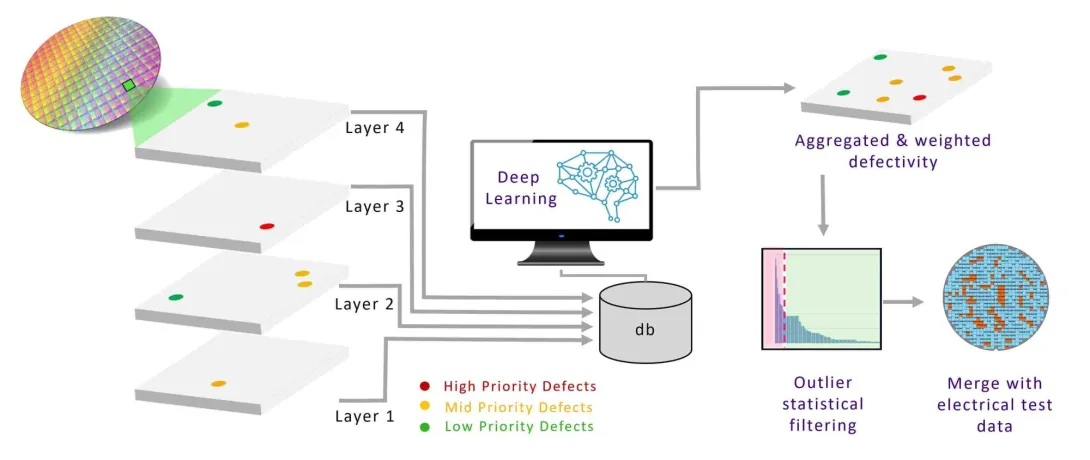
Figure 4. Inline Defect Part Average Testing (I-PAT) scores individual die based on the statistical probability of containing a killer or reliability defect. This data is fed forward to quality and test engineers to be used in conjunction with electrical test data.
Innovating with mstar
Risk is to be avoided at all costs on our roadways, and chip reliability is fundamentally critical to achieving stringent automotive safety standards. There’s a huge opportunity before the automotive and semiconductor industries to elevate Zero Defect initiatives to new heights of reliability and cost effectiveness. Working collaboratively with our partners in the growing mstar ecosystem, KLA is proud to help lead the development of technologies promoting smarter cars that prioritize passenger and pedestrian safety above all.